Up Next

Even if Formula 1 teams carry over some parts from last year into their 2024 car designs, what really can transform a car are the big items that have to be changed to alter the overall architecture of the car.
This includes the chassis, rollover bar structure, side-impact structures, nose, fuel tank location and shape, gearbox housing and rear crash structure.
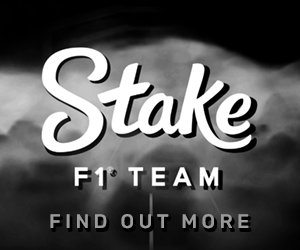
All of these will require new crash or structural load tests to meet the FIA’s safety requirements - a nail-biting experience where one failure can set a team back dramatically.
Getting down to the minimum weight limit of 798kg is not easy, so the teams will also be pushing to reduce the weight on every individual car component, be it a composite structure, a bolt, a nut or a washer, everything needs to be looked at in detail.
There are in excess of 4000 parts spread across the car, so a 1% saving on each item ends up reducing the car weight by 7.9kg.
But there is always a compromise regarding reliability and confidence in passing those structural tests. It’s great if you have one area that you can focus on to save weight, or better still have one component that you don’t really need.
However, that is seldom the case and when it comes to the third year of a set of regulations you know what is structurally required so it’s normally about dotting the I’s and crossing the T’s on every single component.
If you don’t try you won’t succeed so most teams will push the limits in all these areas.
The sheer manpower that an F1 team now has allows them to look at the designs in minute detail. Everything will go through Finite Element Analysis (FEA) and if they are going off the beaten track, teams will also build several initial test components, especially if the geometry is significantly different, to verify that analysis so that when they rock up with the FIA in attendance for the actual tests they will have the confidence that it should all be plain sailing.
But if you are really pushing the limits to save weight, one little slip in the construction process and you can end up bringing the chassis back to the factory in a rubbish bag.
The risky tests are the impact tests. When you see the trolley with the chassis sitting on it heading for what looks like a solid wall, it definitely raises the heartbeat.
But over the years the understanding has increased dramatically. Now the wall isn’t solid, it in itself will have an impact absorption panel between the plate that the nose impacts and the actual solid wall.
This won’t play a part until the chassis sees in excess of the maximum ‘g’ levels that the test has to withstand. If it gets there, this panel will crush and hopefully save the chassis from destruction.
As for the load tests, you can control them reasonably well. They are normally load-versus-deflection, so your FEA should have given you a set of figures to work to. If the deflection increases versus the load being applied doesn’t match your initial prediction, then you can simply stop the test and try again at a later date. You just have to be careful that you don’t run out of those later dates.
With the computerised material cutting tables that the teams, or their suppliers, all have it means that the manual input to a carbon composite component is much reduced. However, the risk is still there as all the individual flexible carbon sections are still manually assembled.
If you are trying to reduce the overall weight, one area to focus on is the carbon overlaps. You need a certain amount of overlap to transmit the load from one piece of cloth to another. You can minimise these, but as you do that the risk level goes up, so it’s the old story of compromise. This one is down with the weight, versus up with the risk.
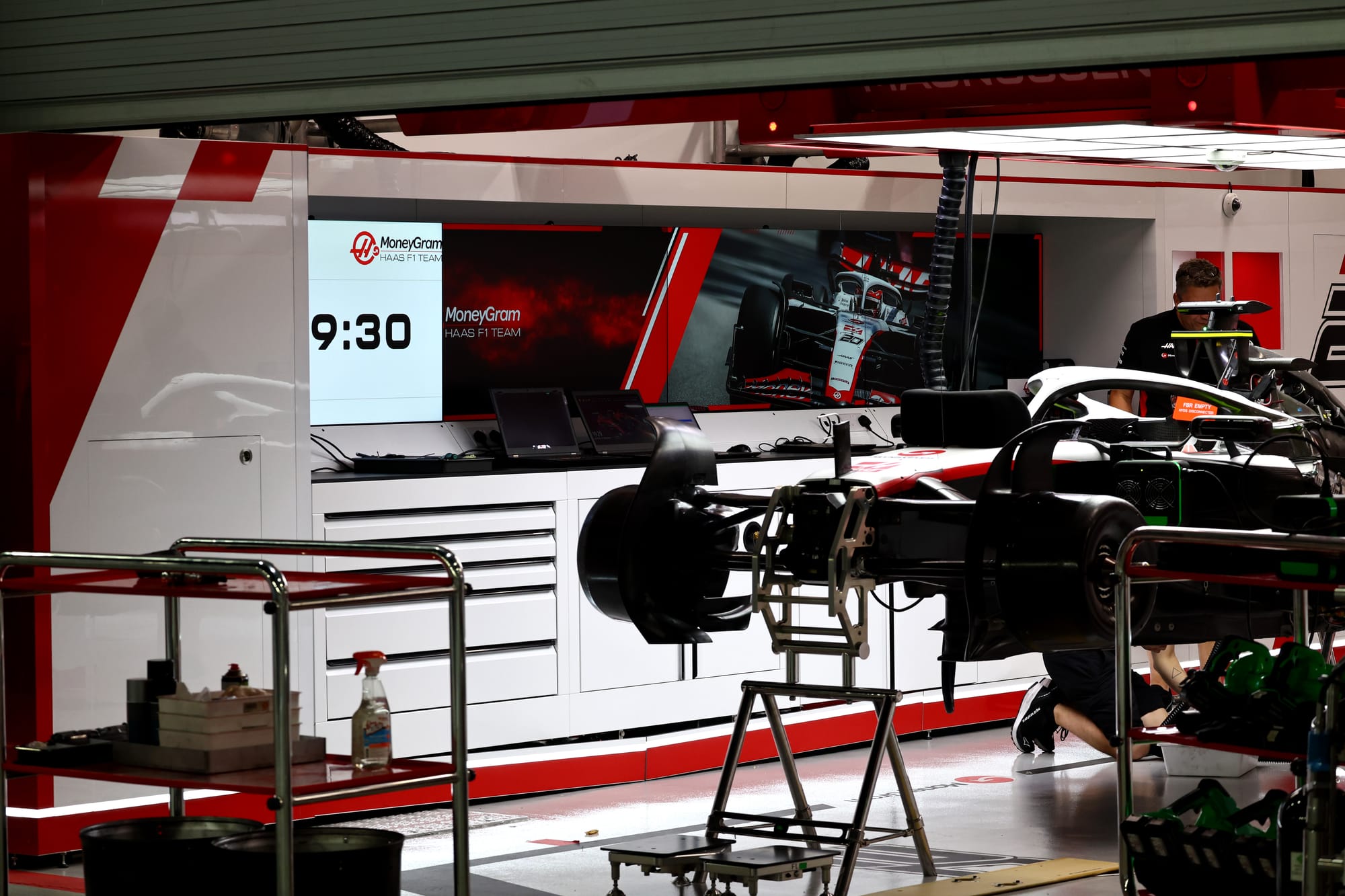
Actually, it’s not only motorsport that has moved on with this sort of technology and writing this column reminds me of my first job when I left school at 15. It was in a shirt factory and I was working on maintaining the machinery. We had a huge layout table for the rolls of material to be laid out on, then the ladies working there would put all different-size paper patterns on the material to minimise the waste. They'd mark the material around the edge of the pattern with chalk and then cut it out with a pair of scissors.
Then it would go to another area to sew all the edges together and voila you had a shirt. Now, that will all be done on a computerised cutting table and I’ll bet the ones used in the shirt factory came long before the ones used in F1.
In the early days of my F1 career in the 70s and early 80s, we didn’t have any real FIA structural tests, it was all down to each team to build what they thought was a safe enough car. Some were and some unfortunately weren’t. The first frontal crash test was introduced in 1985 and the FIA started pushing the levels of testing required before a car could race.
On many occasions, teams were actually at the first race waiting for news on the outcome of some of those final tests from back at base. Some teams would even attempt to get a dispensation to allow them to race if they hadn’t quite met the full requirements of these tests. It was a different time back then, much more ‘stick your finger in the air to see which way the wind was blowing’.
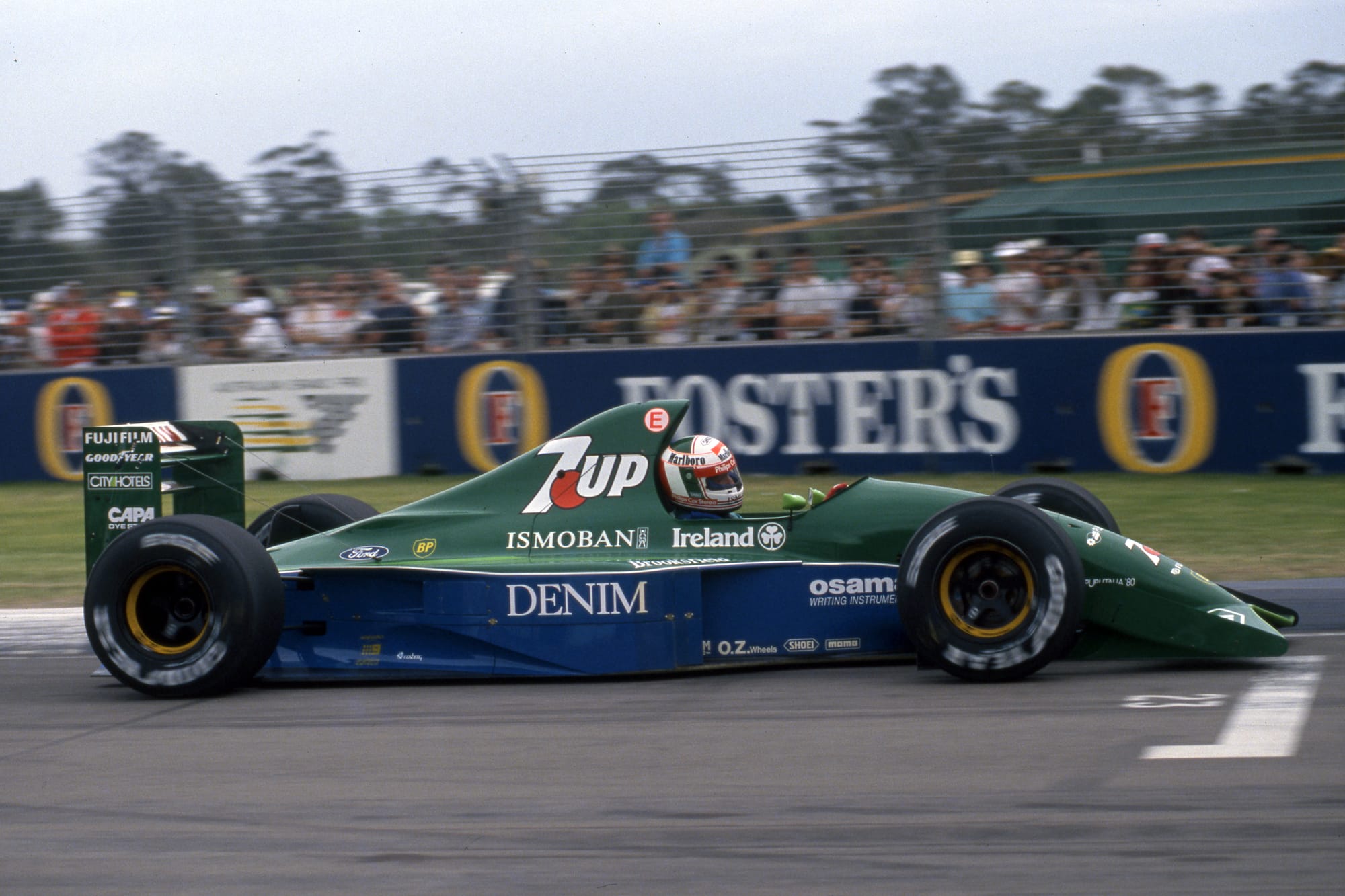
As far as the structural tests are concerned, the amount of tests and the loads involved have probably quadrupled since the mid-90s. Since 2012, you also have to have a clean bill of health before the car can actually be used in pre-season testing, so that means that when the car runs for the first time it has met all the FIA’s safety requirements and you are safe to go.
As far as wings and bodywork deflection are concerned, that is an ongoing process. Other than a wing falling off these tests are not as high a safety concern, it’s more performance-related or because of the flexible bodywork regulations. This is still a grey area because everything must flex a little, but as long as you pass the load versus deflection tests in the specified areas then you meet the FIA’s requirements. That doesn’t stop a team from pushing into the grey areas if it might just help the car’s overall performance.
After all that, the big questions is are you on, or ideally under, the minimum weight limit? Remember, on an average circuit 10kg equates to around three-tenths of a second per lap. That is potentially the difference between pole and around fifth or sixth on the grid. But the more important question is whether it is fast enough.
If the answer to either of those questions is ‘no’ then you start the process all over again with your development priorities.
With 24 races this year, your performance will be judged roughly every two weeks, so unlike many other businesses there is in reality no place to hide.
If you're not ready or your development plan is not well scheduled, the races won’t wait for you.